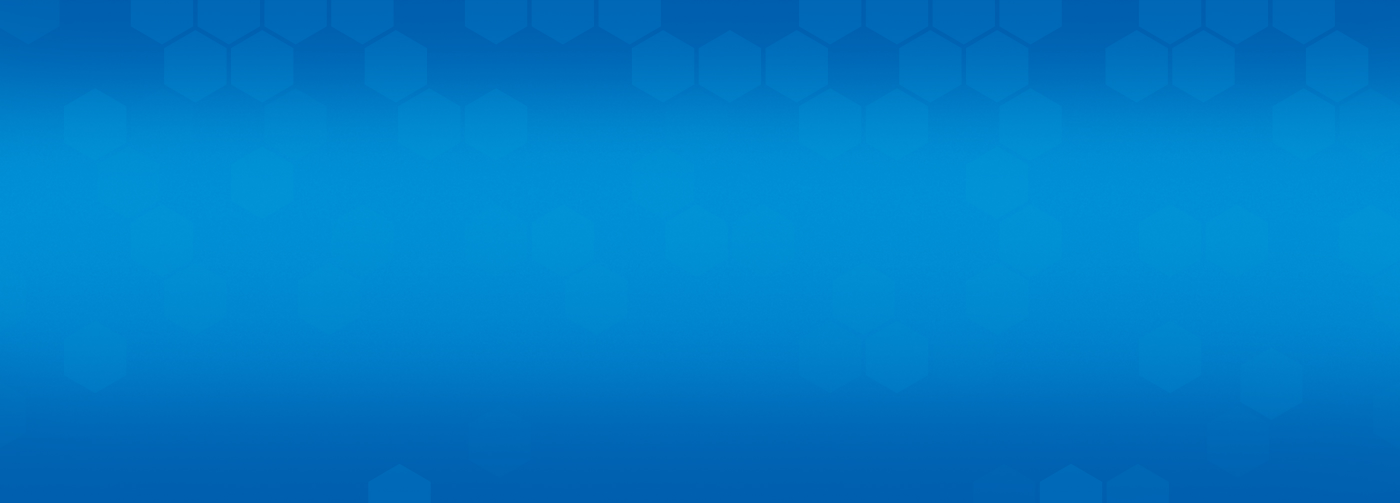
Fluidics
Through strategic partnerships, we engineer innovative fluidic components and subassemblies that result in optimized optofluidic systems. Check out our customer case study below to see how partnership is the key to innovation for your fluidic systems.
Our customer needed help simplifying a complex fluidic instrument that had components spread out across the floor-standing unit, making it a challenge to assemble and service. Their instrument design was also large and didn’t lend itself to using manifolds to consolidate. As a consequence, mistakes were occurring during assembly and the unit required increased service visits. Our customer asked us to find a solution that would prevent costly mistakes and ensure the right connections were being made.
Our support team collaborated with the customer to review their fluidic schematics and pinpoint the key challenges caused by components, assemblies, and replacement frequencies. From there, we were able to devise a plan to significantly simplify their instrument using custom tubing assemblies and color-coded fittings, including our Intuitive Torque-Limiting Fitting, to match each individual component. With this strategy in place, the customer’s assemblers and service groups were no longer forced to repeatedly trace tubing back to the origin to make connections, as the improved design made the process simple and highly efficient. Ultimately, our team created over one hundred unique part numbers and drawings to fully outfit the instrument.