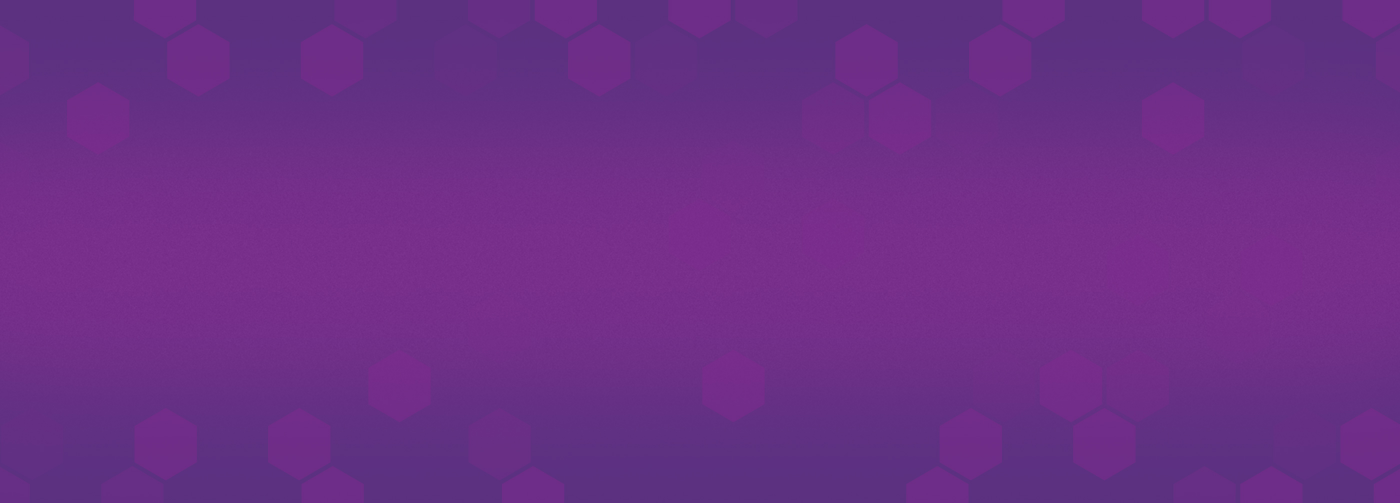
Chemical compatibility in your application is key. If incompatible chemicals contact a fitting in your instrument, your flow path could be compromised. There are many sources for up-to-date information regarding chemical compatibility including the manufacturer of the fittings you have chosen to use. We highly recommend you refer to one of these sources before finalizing your fittings selection.
Full story
We celebrate International Womens Day by honoring the women of IDEX who are part of a global workforce. Check out this story about our CNC Machinist, Lynn Baker.
Full story
Check out our case study where time-to-market was key for the customer. We were able to deliver a custom manifold with iterations made during development
Full story
Using an optical profilometer and microscopes, our team of experts analyze the critical components of rotary shear valves to design your best flow path.
Full story
Overcome misalignment and poor flow by partnering with our team of experts at IDEX Health & Science to evaluate and optimize your valve design.
Full story
With the help of a SmartSkim machine, IDEX Health & Science can now recycle coolant onsite, reducing wastewater production by 85%.
Full story
Share your best scientific images that express the art of fluorescence in our optics photo contest.
Full story
Engineered for robustness in microbore UHPLC applications, learn more about our column with extremely smooth ID surface finish and 40K packing pressure.
Full story
When temperature or pressure of a reagent changes, bubbles will form in the flow path. Discover how degassing enhances the accuracy of 3 instruments.
Full story
Check valves are critical to HPLC pump performance, as they prevent any backflow and ensure maximum pumping efficiency. With the right combination of the design parameters to material selection, based on application needs, optimal performance of the check valve can be achieved.
Full story